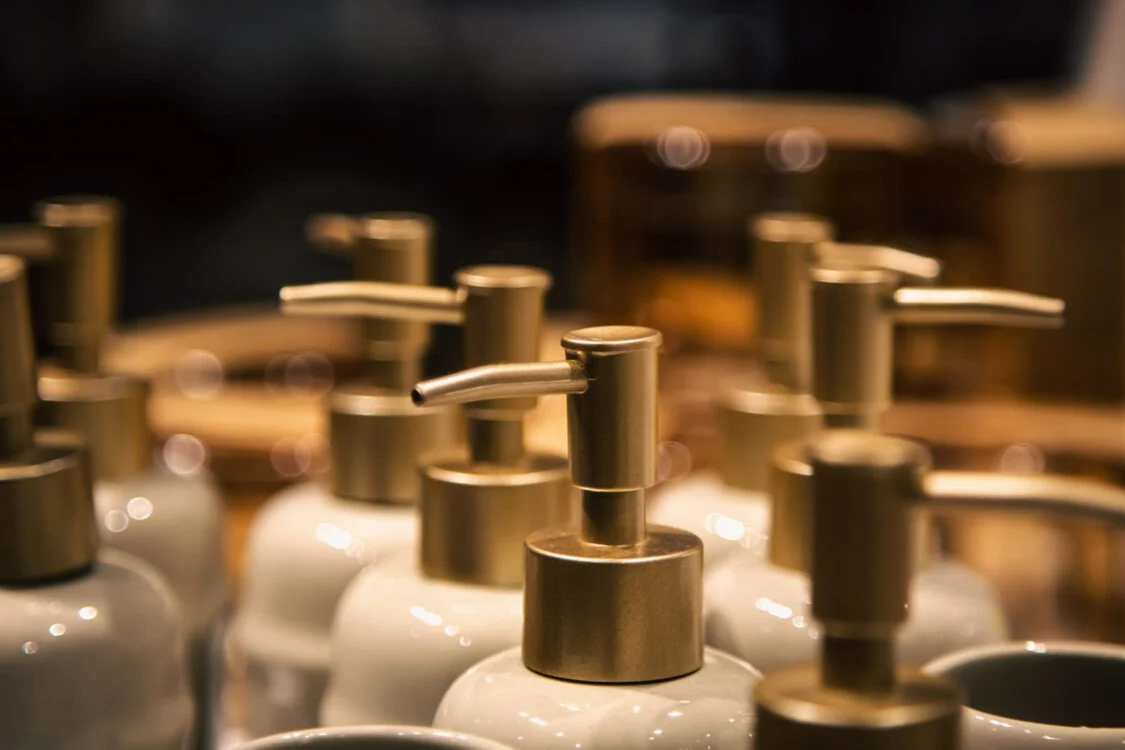
Companies in the cosmetology and aesthetics sector can benefit from RDC 48/2013 to improve the quality of their products, thus contributing to the adequacy of the entire market to the regulatory rules of the National Health Surveillance Agency (Anvisa).
From an economic-financial point of view, following a regulation that provides for good manufacturing practices, while requiring quality control and assurance, protects the manufacturing company from legal damages, strengthens brand loyalty and increases the commercial appeal of the product .
As the RDC itself says: The system for quality management must cover the organizational structure, procedures, processes, resources, documentation and activities necessary to ensure that the product conforms to the intended quality specifications.
To this end, all quality-related activities must be documented. Therefore, it is mandatory to prepare the Good Manufacturing Practices Manual and all procedures.
RDC 48 considers it of fundamental importance that the production of cosmetics is directly related to quality assurance and control, as well as good manufacturing practices. Therefore, the standard reinforces the principles that should guide the Quality Management System (QMS) in companies that manufacture personal hygiene products, cosmetics and perfumes.
It is also worth noting that RDC 48 determines that the manufacturing company must qualify its suppliers, which can be done through:
- Evaluation of the supply history,
- Preliminary assessment through questionnaire
- Quality audits.
As a norm that prioritizes quality in personal hygiene products, cosmetics and perfume, the RDC includes in its text the rules that determine how to apply good manufacturing practices. Cosmetic products can trigger adverse reactions, due to improper use, toxic or irritating substance content above the acceptable level, such as cleaning and sanitizing products.
Cleaning validation is, therefore, an obligation of RDC nº 48/2013, which deals with good manufacturing practices in the cosmetic industry. Its importance is to avoid cross-contamination from previous batches and residues from the cleaning process (detergents and rinsing solution), and microbiological contamination. Only validation guarantees that the cleaning process can ensure that the residues are within predetermined acceptable limits.