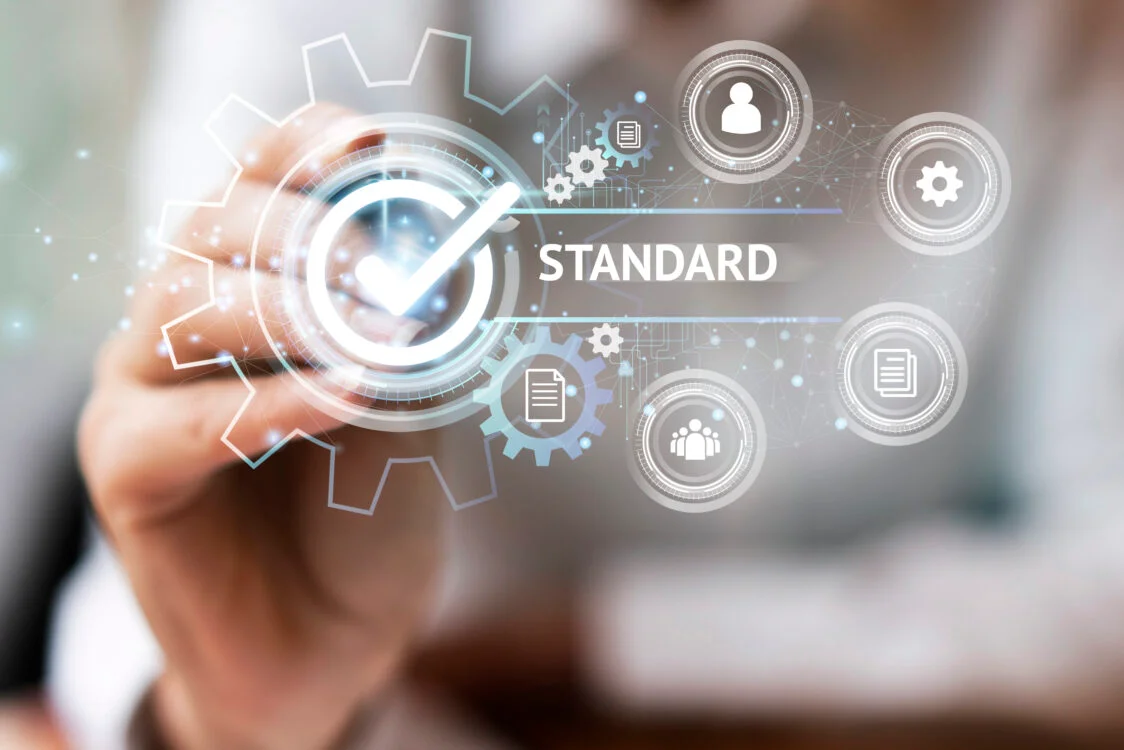
The implementation of ISO 9001 can present several challenges for companies. Some of the common challenges include:
- The implementation of ISO 9001 can present several challenges for companies. Some of the common challenges include:
Resistance and lack of employee engagement: Resistance to change and lack of employee engagement can make it difficult to implement ISO 9001 effectively. Of Quality. - Complexity and lack of understanding of requirements: ISO 9001 has detailed requirements that can be complex to understand and implement. Lack of understanding of the requirements can lead to wrong approaches. It is necessary to invest in training and specialized support such as Klaston’s to guarantee a correct interpretation and effective implementation of the requirements.
- Integration with existing processes: ISO 9001 requires that the organization’s processes are documented, monitored and improved. Integrating these requirements with existing processes can be challenging. An effective approach involves mapping and analyzing current processes, identifying gaps and making necessary adjustments to align with the requirements of the standard.
- Ongoing maintenance of the quality management system: ISO 9001 requires ongoing maintenance of the quality management system, including internal audits and performance reviews. Ensuring the dedication of resources and time to these activities is a common challenge. Creating a schedule of activities, establishing clear responsibilities and prioritizing quality are measures that can help overcome this challenge.
- Preparing for audits and certifications: Preparing for external audits and certifications is an additional challenge. It is important to have adequate records and documentation, implement corrective actions when necessary, and conduct periodic internal audits to ensure compliance with the requirements of the standard.
To overcome these challenges, it is essential that top management is committed, that there is a systematic approach to implementation, that adequate resources are allocated, and that communication and training are effective. It is also important to seek the support of specialized consultants, learn from the best practices of other companies and maintain a continuous focus on improving the quality and efficiency of processes.